Ein bahnbrechendes neues Projekt mit französischer Bautechnik und spanisch / amerikanischer Hydrauliktechnologie. |
Das Millau-Viadukt in Frankreich -- Die höchste Talbrücke der Welt
|
Im Juni letzten Jahres hat Enerpac Hydraulic Technology den Zuschlag für den Vertrag zur Lieferung des Hydrauliksystems
zum Anheben der temporären Pfeiler und zum Verschieben des Brückenüberbaus beim Bau der Millau-Hochbrücke erhalten. Zur Zeit befindet sich dieses Projekt in der Realisierungsphase. Ein Meilenstein der Geschichte: Es geht um die Entstehung der höchsten Hochbrücke der Welt. |
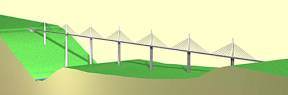 |
Die Voruntersuchungen für das Millau-Hochbrückenprojekt begannen bereits im Jahr 1988; mit dem Bau dieser Hochbrücke sollte den Verkehrsproblemen auf der A75, der Autobahnverbindung zwischen Paris und Barcelona, ein Ende gesetzt werden. Nach der Erwägung diverser möglicher Routen hat
sich die CETE ('Center for Technical Equipment Studies') von Aix-en-Provence am 28.Juni 1989 für die 'mittlere' Route entschieden, die östlich von Millau den Fluss Tarn kreuzt. Diese sogenannte 'Hochbaulösung' beinhaltete eine große Hochbrücke, die das Flusstal des Tarn 'überspannen' sollte, ohne sich dabei
abzusenken; somit wurde kein Tunnel benötigt. Dies war die seit 1991 bevorzugte Option, da sie nur eine minimale Umweltbeeinträchtigung mit sich bringt und zudem eine bessere Sicherheit bietet als die andere Alternative. Die Detailuntersuchungen begannen im Jahr 1993 und im Jahr 1994 wurde ein beschränkter Wettbewerb ausgeschrieben. Daran haben sich füf Architektenteams beteiligt.
Gewonnen hat die Alternative, die von dem Team der französischen Ingenieure Sogelerg, EEG, SERF und Foster im Jahr 1996 vorgelegt wurde.
|
Vom Design bis zum Bau
Fosters Design, mit seiner beeindruckenden Ästhetik und Größe,ließ sich nicht gerade leicht realisieren, ohne dabei in finanzielle Schwierigkeiten zu geraten. Diese Brücke ruht auf zwei Widerlagern und sieben Pfeilern und überspannt insgesamt eine Strecke von 2460 m über dem Flusstal des Tarn. Sie erreicht dabei in der Mitte eine Höhe von 245 m, mit 204 m langen
Überspannungen zwischen den Widerlagern sowie zwischen dem ersten und letzten Pfeiler. Hinzu kommen 342 m lange Überspannungen zwischen den verbleibenden Pfeilern, wobei die Höhe zwischen 70 m für den ersten und 340 m für den dritten Pfeiler variiert. Die Struktur ist mehrfach verstrebt, wobei vertikale, stimmgabelförmige Hohlbetonelemente zur Unterstützung der beiden Fahrbahnen von der Mitte aus dienen. Diese Fahrbahnen besitzen
eine Gesamtbreite von 27,35 m. Dies ist hinreichend für drei Fahrbahnen in jede Richtung (von denen jedoch zunächst nur zwei benutzt werden sollen) sowie beidseitige Standspuren.
Vom Blickwinkel des Fahrers aus gesehen besitzt die Hochbrücke eine leichte Steigung (3,035 % von Norden nach Süden) sowie eine geringe Biegung (Kurvenradius 20 000 m). In der Mitte beträgt die Höhe über dem Boden 270 m; der Pfeiler genau in der Mitte mit seinen Streben allerdings ist mehr als 340 m hoch; er ist somit 14 % höher als der Eiffelturm.
Zwei Materialien -- Beton beziehungsweise Stahl -- wurden für den Brückenüberbau in Betracht gezogen und untersucht. Schließlich fiel die Wahl auf Stahl als Baumaterial, da sich hierbei die Hochbrücke schlanker gestalten ließ, was nicht nur die Ästhetik verbessert (der Brückenüberbau aus Beton hätte eine Höhe von 4,6 m erforderlich gemacht), sondern auch die Sicherheit zu Gute kommt; und zwar sowohl während der Bauphase als auch beim späteren Einsatz.
|
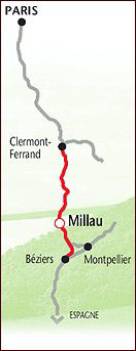 |
Beim Bau wurden 27 000 Kubikmeter Beton, 19 000 Tonnen Betonstahl und 5000 Tonnen Baustahl für die Kabel und Abdeckungen benötigt. Dabei sollte
B60-Hochleistungsbeton für die Pfeiler und die formveränderliche selbstkletternde Metallverschalung zum Einsatz gelangen. Nachdem am 9. Juli 1996 die Entscheidung für die endgültige Konfiguration
des Projekts gefallen war, musste nur noch entschieden werden, wer diese Arbeiten ausführen sollte und in welcher Weise sie auszuführen waren.
Diverse Firmen haben sich an der Ausschreibung für die entsprechende Konzession beteiligt. Das französische Ministerium für Verkehr und öffentliche Bauvorhaben jedoch entschied sich für die Eiffage Group TP (die drittgrößte Firma dieser Art in Frankreich; sie steht größenmäßig an fünfter Stelle in Europa). Daraufhin hat die Eiffage Group TP eine neue Firma (die Compagnie Eiffage du Viaduct de Millau) speziell für diesen Zweck ins Leben
gerufen. Diese neue Firma erhielt eine 75-jährige Betriebskonzession als Gegenleistung für die Finanzierung des Projekts. Die Kostenschätzung (zu Beginn der Bauarbeiten) belief sich auf € 300 000 000, zuzüglich eines
Betrags von weiteren € 20 000 000 für die 6 km weiter nördlich befindliche Mautstation.
|
Der gesamte Bau ist so konzipiert, dass er auch extremen seismischen und meteorologischen Einflüssen standhält; die fehlerfreie Funktion wird für
Zeitraum von mindestens 120 Jahren gewährleistet. Die größten bautechnischen Probleme ergeben sich bei der Erstellung des Überbaus mit einer Masse von 36 000 Tonnen, der aus beiden Richtungen zur Mitte hin vorgeschoben wird. Die Elemente werden in den Produktionsstätten Eiffel,
Lauterbourg und Fos-sur-Mer vorgefertigt, und eine Baugruppe aus 64 Hydraulikhebern wird für diesen Vorschub verwendet. Aus der 342 m langen
Horizontalverschiebung für die sechs mittleren Überspannungen ergibt sich die Notwendigkeit der Installation von fünf temporären Pfeilern,
deren Bau der spanischen Division von Enerpac übertragen wurde. |
Ein Hydrauliksystem zum Anheben der temporären Zwischenpfeiler |
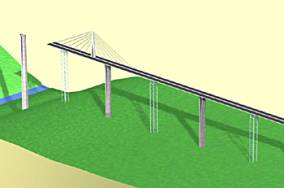 | Sieben temporäre Zwischenpfeiler müssen für den Vorschub des Brückenüberbaus zwischen den definitiven Pfeilern eingesetzt werden. |
Bei der Auslegung der Millau-Hochbrücke hat Eiffel, eine Tochtergesellschaft der Eiffage Group, die sich auf den Stahlbau spezialisiert, geschätzt, dass sieben temporäre Zwischenpfeiler zwischen den definitiven Pfeilern eingebaut werden müssen, um den Brückenüberbau während des Baus 'vorschieben' zu können.
Zwei der temporären Pfeiler (am jeweiligen Ende der Struktur) werden direkt mit einem Kran installiert, da sie nur 20 m beziehungsweise 12 m hoch sind. Die Höhe der übrigen 5 Pfeiler liegt jedoch
zwischen 87,5 m und 163,7 m. In diesem Zusammenhang wurde ein Teleskopsystem zum Anheben der temporären Pfeiler entwickelt, wobei der Hydraulikteil von der örtlichen Enerpac-Niederlassung in Spanien realisiert wird.
Sobald ein Pfeiler angehoben worden ist, wird die gesamt Maschinerie, einschließlich des Hydrauliksystems, demontiert und entsprechend versetzt, um den nächsten Pfeiler zu installieren.
|
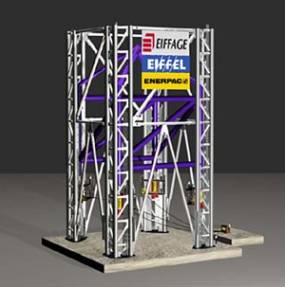 | Teleskopsystem zum Anheben der temporären Pfeiler |
Das Teleskopsystem besteht aus zwei Teilen:
- Zu erwähnen ist zunächst die Kubikstruktur mit 12 m großen Bodenplatten. Diese beinhaltet das gesamte System, ausgestattet mit 'Zahnstangen', wobei an den Scheitelpunkten eine Meter-Skala vorhanden ist.
- Zweitens besteht der Hubmechanismus aus dem Hydraulikzylinder und dem hydraulischen Steuersystem. Die Hydraulikzylinder sind an den vier Scheitelpunkten des Kubus installiert und an Stützen verankert, die mit der Zahnstange verbunden sind und aufgrund des sukzessiven Einschubs von
Sperr-Hemmschuhen in die Zahnstange die vertikale Verschiebung der Pfeilerstrukturen wie auch der Hydraulikmaschinen nach Maßgabe der jeweiligen Maschinenstruktur ermöglichen.
Hubstufen von 1000 mm
Das Funktionsprinzip ist einfach: die Stützen für die Zylinder sind über Hemmschuhe in der Zahnstange verankert, während die Struktur der Pfeiler frei ist. Das Bedienungspersonal verwendet Steuerelemente mit einer
umfassenden Software, die alle nur möglichen Sicherheitsoptionen bietet. Diese beginnen mit dem Verpumpen des Öls zu den Zylindern und schieben damit die Plungerkolben hoch, die wiederum gegen die Struktur der Pfeiler
angedrückt werden. Somit heben die Zylinder die Pfeilerstruktur bis zur nächsten Zahnstangenperforation an. Der Zylinderhub beträgt 1100 mm und die 'Zahnstange' ist alle 1000 mm eingekerbt, und zwar so, dass insgesamt
100 mm zur Kompensierung möglicherweise eintretender unvorhergesehener Umstände verfügbar sind. Jeder Hydraulikzylinder besitzt seine eigene Steuerung mit
der Option einer sofortigen Sperre; hinzu kommen Sensoren aller Art,um unvorhergesehene Bedingungen, die eine Nachstellung beim Anheben der Pfeilerstruktur erfordern, sofort erkennen zu können (Wind, Temperatur,
etc.). Dabei wird jeder einzelne Zylinder unabhängig angehoben. Sobald die gewünschte Höhe erreicht ist, wird die Pfeilerstruktur mit Hemmschuhen gesichert; dann werden die Hemmschuhe zur Unterstützung des Zylinders
gelöst. Die Plungerkolben werden daraufhin zurückgezogen und die Zylinderkörper zusammen mit ihren Stützen bis zur unmittelbar darüber liegenden Zahnstangenperforation angehoben, wo sie dann mit Hemmschuhen gesichert werden. Auf diese Weise werden sowohl die Pfeilerstruktur
wie auch die Hydraulikmaschinerie um 1 m angehoben. Danach wird dieser Vorgang wiederholt, bis das erste Element aus der Maschinenstruktur herausragt (unten gesperrt).
Sobald es seine Funktion erfüllt hat und da es jetzt weniger wiegt, wird das Hydrauliksystem mit einem Kran ganz bis unten abgesenkt; sobald es den Boden erreicht hat, wird ein zweites Pfeilerelement darauf befestigt und
man fährt in der gleichen Weise fort, bis der gesamte temporäre Pfeiler fertiggestellt ist. Daraufhin kann der Brückenüberbau über den neuen Pfeiler geschoben werden.
Prozeßsteuerung
Dieser Hubvorgang erfordert eine sehr präzise Steuerung. Daher sind die Hydraulikzylinder mit einem internen Positionsgeber ausgestattet. In ähnlicher Weise sind auch die Druckleitungen mit Druckgebern versehen, die
ausnahmslos zum Schutz vor schlechtem Wetter, Schmutz, Feuchtigkeit usw. intern eingebaut sind.
Alle Informationen laufen an einem Steuerpult zusammen, das über einen PLC
die Daten verarbeitet und entsprechende Befehle an die Elektroventile sendet. Somit werden die Zylinder über ein etabliertes Programm angehoben.
Dank des Steuerpults ist das Bedienungspersonal jederzeit über die Höhe und Position der einzelnen Zylinder unterrichtet und kann bei Bedarf die weitere Bewegung stoppen, wenn gewisse Systemvariablen die vorgegebenen Grenzwerte
überschreiten. |
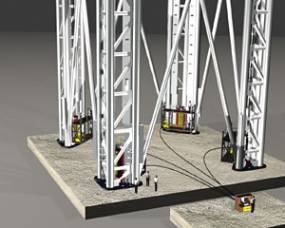 | Das hydraulische System von Enerpac |
Jeder einzelne Zylinder besitzt seine eigene Hydraulikpumpe. Somit kann jeder Zylinder bei Bedarf individuell angesteuert werden; allerdings unter der Voraussetzung, dass ein umfassendes Anforderungsprotokoll erstellt und
von der Zentralapplikation genehmigt wird.
Das Bedienungspersonal an beiden Enden der Struktur hat Zugang zu den Steuerelementen, die an die Zentralsteuerung angeschlossen sind. Auf diese Weise verifizieren diese Elemente während des Prozesses das Einlegen beziehungsweise den Rückzug der Hemmschuhe. Sobald das entsprechende Signal
eingeht, gibt die Person an der Zentralsteuerung den Befehl zur Fortsetzung des Prozesses.
|
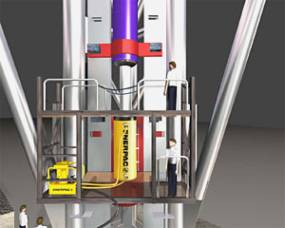 | Das System ist so konzipiert, dass Höhenabweichungen von über 3 mm nicht erlaubt sind. Ebenfalls ausgeschlossen ist eine maximale Lastdifferenz von mehr als 5% zwischen den Zylindern. |
Ebenfalls vorhanden sind Monitore zur Überwachung von Ölpegel und Temperatur sowie Alarmvorrichtungen, die bei unvorhergesehenen Umständen (Druckabfall, Kabelriss usw.) den Vorschub stoppen.
Technische Spezifikationen
Zum Hydraulikteil der Maschine gehören vier Zylinder, jeder mit einer eigenen Pumpe, die zentralisiert an ein zentrales Steuerpult angeschlossen sind. Jede Baugruppe besitzt eine Schubkapazität von 511 Tonnen, was somit
insgesamt eine maximale Schubkapazität von 2044 Tonnen ergibt. Bei normalen Betriebszyklen sollte ein Sollwert von 420 Tonnen normalerweise nicht überschritten werden. Somit ist diese Baugruppe mit einem erheblichen
Sicherheitsspielraum konzipiert worden. Der Solldruck beträgt 700 Bar und der Zylinderhub ist, wie erwähnt, 1100 mm. Eine Überlast von 675 Tonnen ist bei ausgefahrenem Plungerkolben zulässig; bei eingefahrenem Plungerkolben
gilt entsprechend ein Wert von 1500 Tonnen.
Das gesamte Steuersystem (mit der Verkabelung, dem Steuerpult, den visuellen Displays usw.) ist gegen Außeneinflüsse und elektromagnetische Störungen
sowie vor Unfällen und möglichen Stößen bei der Installation und auch während des Betriebs geschützt.
|
Enerpac, Mitglied der Actuant -- Firmengruppe mit Stammsitz in den USA, blickt auf eine lange Geschichte im Hinblick auf die Herstellung von
Hochdruck-Hydraulikgeräten aller Art sowie Systemen für die Industrie und das Baugewerbe zurück, und das seit den allerersten Anfängen mit der Herstellung von Stoßdämpfern für den legendären Ford T. |
Interessante Websites:
http://www.viaducdemillaueiffage.com/
http://www.enerpac.com
http://www.eiffel.fr/
Weitere Informationen erhalten Sie bei:
Enerpac bv Irene Kremer PO Box 269 NL - 3900AG Veenendaal Niederlande Tel.: +31 318 535911 Email: irene.kremer@enerpac.com
|